A spindle is a part of the axle. It is a machined part whose primary purpose is to support the bearing races (see Figure 3.11) for the hub. Figure 3.10 shows the most common spindles used in the trailer industry for capacities of 1800-lbs, 3500-lbs and 5200-lbs. While other spindles are the available for various reasons, higher capacities and special uses, capacities shown here cover just about any application, up to extra heavy duty trailers. You would be doing yourself a favor by selecting one of the more common grinds shown here, since replacement bearings, seals and hubs are very easily found and readily available from bearing stores and many trailer supply outlets.
Spindles for trailers are quite different than automobile spindles. The more reliable ones are much “beefier” than auto spindles. Considering the difference in load requirements, this should be expected. An automobile spindle carries 1/4 of a 4000-lb load (plus or minus) or about 1000-lbs. A typical midrange trailer carries 1/2 of 2000 to 3500-lbs (1000 to 1750-lbs). This loading difference is also important when selecting wheels and tires.
Spindles are rated for a specific load using similar techniques as used for computing axle strengths. Spindle strength is usually figured and rated separately from the axle. In addition to just plain overloading, spindles can be weakened by excessive heat (from lack of bearing grease or rust), and/or use of positive offset wheels which can increase the bending moment at the spindle. This offset also increases the overhang distance-not something we want to do, as you may have guessed from a few pages back. With a little attention, these situations can be avoided and spindle life increased. Designing a new spindle is not something everyone should undertake considering the bargains in the ones currently available. Besides being inexpensive for what is provided, optimum spindle design is best left to automotive engineers and bearing experts who have had many years of experience in this field.
Spindles are machined to a precise diameter such that the bearing ID will slide on easily with the right amount of clearance. If you experience difficulty installing a bearing, it may be due to a burr on the spindle, which can be removed with a very light touch from a file or piece of sandpaper. Be sure to then clean the surface with a solvent soaked rag before attempting to slide the bearing on again (small filings can accelerate bearing wear).
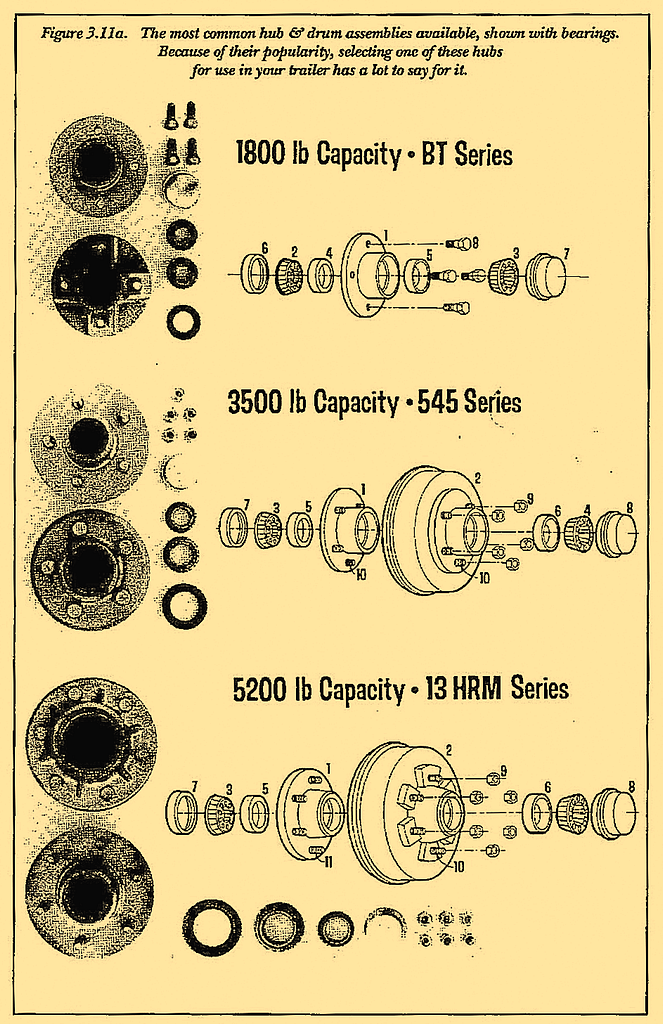